RENDERING SYSTEM
Continuous Dry Rendering
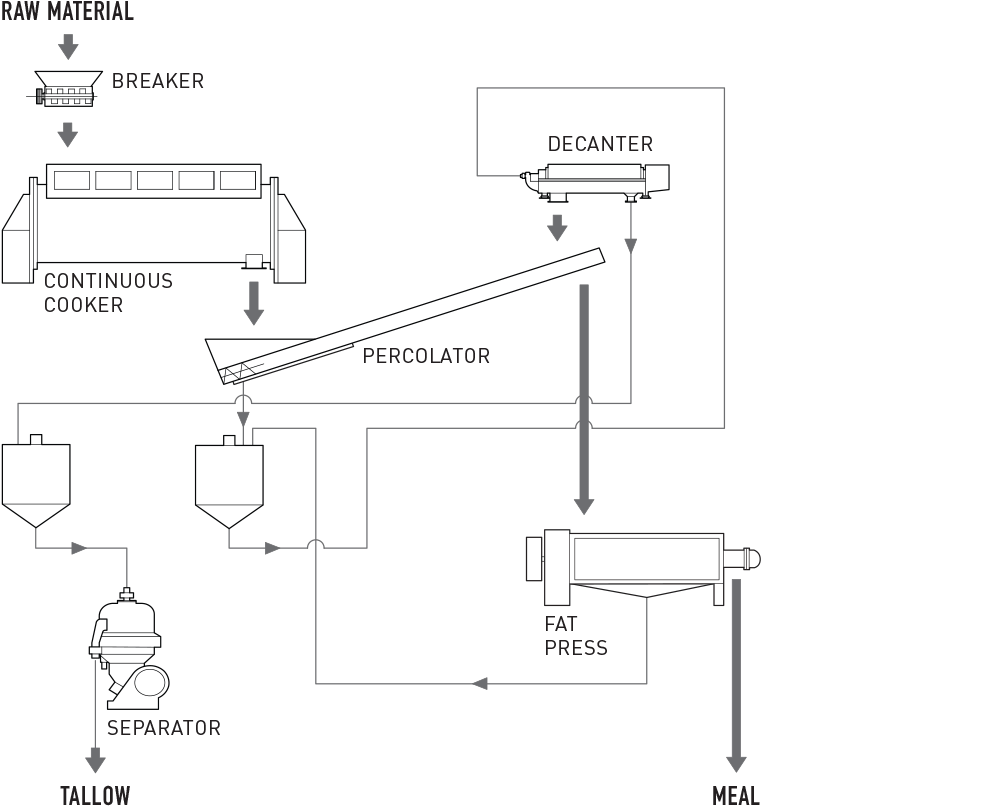
The Rendertech Continuous Dry Rendering System (CDR) is a dry rendering process suitable for plant capacities of 2 tonne/hr and above. It handles a wide range of raw materials and is a simple but flexible process. Compared to batch systems, Rendertech’s continuous system can significantly reduce energy and labour requirements. At the heart of the Rendertech CDR system is the Rendertech Continuous Cooker.